Gli anni 2015 e 2016 possono essere considerati come il punto di svolta per la stampa diretta in metallo (DMP, Direct Metal Printing) nel settore aerospaziale, grazie al progressivo avanzamento della tecnologia oltre la prototipazione, fino alle parti di produzione e agli assiemi pronti per il volo.
In tale periodo, Airbus Defence and Space ha lavorato con 3D Systems per arrivare a un'innovazione importante: il primo filtro a radiofrequenza (RF) stampato in 3D testato e convalidato per l'uso nei satelliti per le telecomunicazioni commerciali. Il progetto è stato basato su una ricerca finanziata dall'Agenzia Spaziale Europea (A0/1-6776/11/NL/GLC: Modellazione e progettazione di componenti ottimizzati per guide d'onda mediante le tecniche di produzione 3D).
I filtri in guida d'onda o RF in metallo sono stati introdotti circa 50 anni fa con i primi sistemi di comunicazione spaziale. I filtri agiscono come agenti del traffico: consentono alle frequenze di determinati canali di passare, mentre rifiutano quelle provenienti da segnali al di fuori di tali canali.
Una tendenza importante del settore è di incrementare la capacità operativa di un satellite mediante fasci multipli. Un satellite ad alta capacità, come l'Eutelstat KA-SAT prodotto da Airbus Defence and Space, supporta circa 500 filtri RF e oltre 600 guide d'onda. Molti sono progettati appositamente per gestire frequenze specifiche.
Necessità di soddisfare requisiti cruciali
I satelliti per telecomunicazioni sono la dimostrazione dello sforzo incessante del settore aerospaziale volto a ridurre il peso. Infatti il costo per collocare un veicolo in un'orbita geostazionaria si aggira intorno a $20.000 al chilogrammo. Altre importanti priorità sono l'innovazione costante nella progettazione e la riduzione dei tempi di produzione, dato che la maggior parte dei satelliti è costruita per durare 10–15 anni.
Tali priorità fanno sì che i satelliti per telecomunicazioni siano i candidati ideali per la stampa diretta in metallo. La stampante ProX® DMP 320 di 3D Systems, utilizzata per il progetto riguardante i filtri RF di Airbus, permette ai produttori di diminuire il numero di parti da assemblare, migliorare la funzionalità mediante forme e superfici impossibili da realizzare con i metodi tradizionali, accorciare i tempi di produzione e diminuire i costi per i progetti personalizzati, nonché ridurre il peso mantenendo o persino migliorando la resistenza dei materiali.
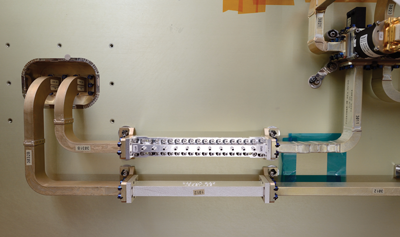
Nuova applicazione per stampante comprovata
Lo stabilimento di 3D Systems situato a Lovanio, in Belgio, utilizza la stampante ProX DMP 320 di 3D Systems sin da quando la macchina era allo stadio beta. Progetti di successo riguardano l'ottimizzazione topologica, la riduzione del peso e l'accorpamento delle parti per il settore aerospaziale, quali staffe e raccordi per montanti destinati ai satelliti per telecomunicazioni. Il progetto di Airbus Defence and Space ha rappresentato la prima applicazione di 3D Systems, Lovanio, nel campo dei filtri RF.
La stampante ProX DMP 320 è stata progettata per offrire elevata precisione e alto rendimento in ambienti di produzione molto esigenti, 24 ore su 24, 7 giorni su 7. L'ampia gamma di leghe LaserForm (titanio, acciaio Inox, alluminio, nichel cromo e cromo-cobalto) è stata formulata e ottimizzata per questa stampante in metallo, allo scopo di fornire parti di alta qualità e proprietà uniformi.
I moduli di produzione intercambiabili offrono maggiore versatilità delle applicazioni e tempi di inattività ridotti quando si passa da un tipo di materiale a un altro. Una camera di costruzione controllata assicura che ogni parte venga stampata con proprietà, densità e purezza chimica dei materiali.
Straordinaria innovazione nella progettazione
Il progetto riguardante i filtri RF di Airbus Defence and Space dimostra la capacità della stampa 3D di favorire l'innovazione nella progettazione di parti per il settore aerospaziale, che non hanno subito variazioni significative negli ultimi decenni.
Solitamente i filtri RF vengono progettati sulla base di librerie di elementi standardizzati, quali cavità rettangolari e sezioni trasversali di guide d'onda con piegature perpendicolari. Le forme e i raccordi sono determinati dai processi di produzione tradizionali, quali la fresatura e l'elettroerosione. Ne consegue che le cavità per i filtri RF devono essere lavorate a partire da due metà avvitate insieme. Questo comporta un aumento di peso, l'aggiunta di una fase di assemblaggio al processo di produzione e un
controllo di qualità supplementare.
La progettazione di parti per la stampa 3D ha permesso a Airbus Defence and Space di sperimentare geometrie complesse senza aumentare i costi di produzione.
Per progettare i filtri RF stampati in 3D è stato utilizzato CST MWS, uno strumento software di simulazione elettromagnetica 3D, con tempi di ottimizzazione ridotti. Grazie alla maggiore flessibilità di produzione offerta dalla stampa 3D, è stato possibile creare un progetto utilizzando una cavità super-ellissoidale ribassata. La forma particolare ha permesso di incanalare le correnti RF e di ottenere il giusto equilibrio tra il fattore Q, che indica l'efficienza di una guida d'onda basata sull'energia persa, e il rifiuto dei
segnali fuori banda.
“L'innovazione straordinaria sta nel fatto che ora è la mera funzionalità, non la fattibilità, che determina il modo in cui l'hardware verrà progettato”, spiega Koen Huybrechts, ingegnere progettista presso lo stabilimento 3D Systems di Lovanio. “Questo progetto è un classico esempio di come la forma si adatti alla funzione.”
“I vantaggi principali della progettazione monolitica resa possibile dalla stampa 3D sono massa, costo e tempo”, afferma Paul Booth, ingegnere RF per Airbus Defence and Space a Stevenage, Regno Unito. “La massa risulta ridotta perché gli elementi di fissaggio non sono più necessari. La stampa diretta in metallo offre un ulteriore vantaggio a costo zero: il profilo esterno segue più precisamente il profilo interno, pertanto è possibile utilizzare solo il metallo realmente necessario. Il vantaggio in termini di costi e tempi deriva dalla riduzione dei processi di assemblaggio e post-elaborazione.”
Eliminazione dei dubbi riguardo alle superfici
Inizialmente si temeva che la diversa topologia delle superfici delle parti metalliche stampate in 3D rappresentasse un problema, ma i numerosi test condotti da Airbus Defence and Space hanno consentito di dissipare tali dubbi.
“La topologia microscopica di una parte stampata in 3D è diversa da quella di una parte lavorata a macchina”, spiega Booth. “Le superfici lavorate presentano picchi e avvallamenti, mentre una superficie stampata in 3D è costituita da sferoidi fusi insieme, pertanto è caratterizzata da minore spigolosità.”
“La forma sferica delle particelle di polvere utilizzate per la stampa 3D in metallo consente di ottenere una certa ondulazione anziché transizioni nette”, spiega Huybrechts, “ma la possibilità di modellare parti che offrono un filtraggio del segnale più efficace elimina facilmente ogni dubbio riguardo alla topologia delle superfici.”
“Siamo molto soddisfatti del lavoro che 3D Systems ha svolto per noi e molte persone all'interno di Airbus hanno notato la qualità elevata della finitura superficiale”, riferisce Booth. “Abbiamo eseguito alcune scansioni TC a raggi X e siamo rimasti sorpresi dalla densità della parte e dalla qualità della superficie in generale.”
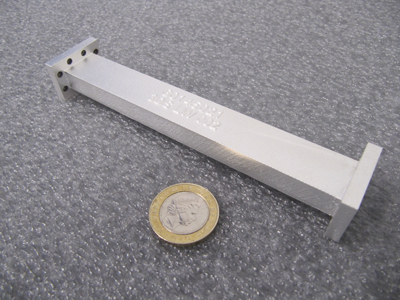
Superamento di test rigorosi
Tre campioni in alluminio ottenuti con la stampante ProX DMP 320 mediante percorsi di elaborazione differenti sono stati testati da Airbus Defence and Space presso lo stabilimento di Stevenage. Speciali test hanno riprodotto le condizioni a cui le parti sarebbero state soggette durante il lancio e la messa in orbita, inclusi urti, vibrazioni, condizioni termiche (come temperature estreme) e condizioni di vuoto. Tutti e tre i campioni hanno soddisfatto o superato i requisiti; le prestazioni migliori sono state ottenute da un filtro precedentemente placcato in argento mediante un processo elettrolitico.
Oltre alla stampa 3D, 3D Systems ha fornito valore aggiunto, estremamente importante per questa tipologia di progetto, inclusi gestione della polvere certificata, controllo del processo per una densità del materiale eccellente, post-elaborazione comprovata e controllo qualità affidabile.
Booth riconosce che l'apporto di competenze specifiche è stato determinante per la riuscita del progetto: “Ci rendiamo conto che il risultato ottenuto non dipende solo dall'uso di una valida macchina per produrre le parti, ma anche dall'accurata comprensione del processo di produzione da parte di 3D Systems.”
Potenziale di ritorno di investimento molto elevato
Ora che il processo è stato convalidato e le parti hanno soddisfatto i più elevati standard aerospaziali previsti da Airbus Defence and Space, l'azienda può valutare il potenziale ritorno sugli investimenti sostenuti per la stampa 3D in metallo. Il progetto offre un ROI che fa brillare gli occhi del direttore finanziario: tempi di completamento più rapidi, costi di produzione ridotti e una sorprendente riduzione del peso pari al 50%.
“La massa è stata ridotta senza la necessità di dedicare tempo all'ottimizzazione”, dichiara Booth, “e può essere ridotta ulteriormente con una progettazione meccanica più incisiva. La minore massa consente di risparmiare sui costi, poiché il razzo consuma meno propellente, e riduce i requisiti in termini di strutture di sostegno, con la conseguente ulteriore riduzione della massa.
“Il successo di questo progetto spiana la strada verso una sempre maggiore integrazione dei filtri RF con i componenti meccanici e termici, al fine di ridurre il numero di parti e la massa totale. Prevediamo inoltre di introdurre altre funzionalità, ad esempio gli accoppiatori di prova, come parte del filtro, o di integrarle direttamente nella produzione delle guide d'onda. Vi sono enormi potenzialità di riduzione della massa, con la conseguente riduzione sia dei costi sia dei tempi di produzione.”